The Fabrication Process: From Raw Material to Operational Equipment
July 22, 2019
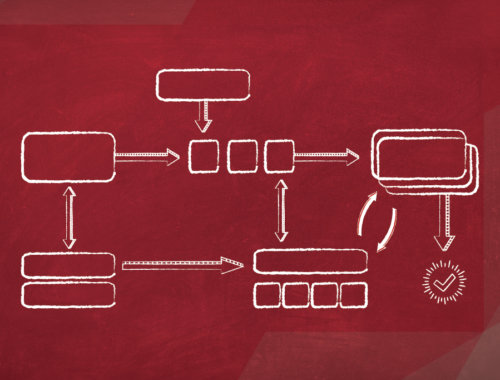
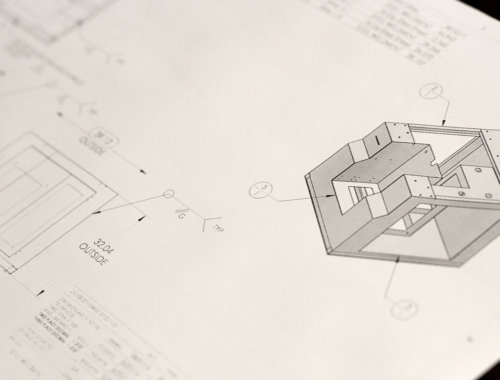
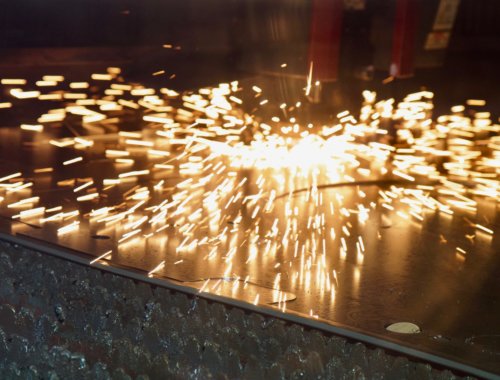
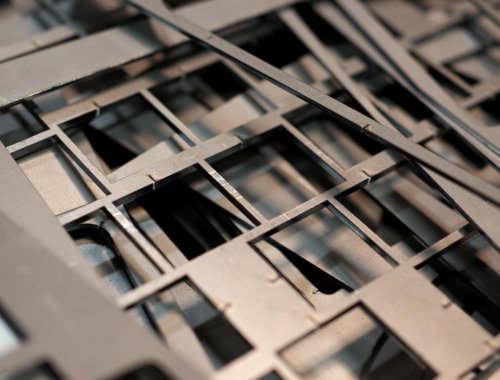
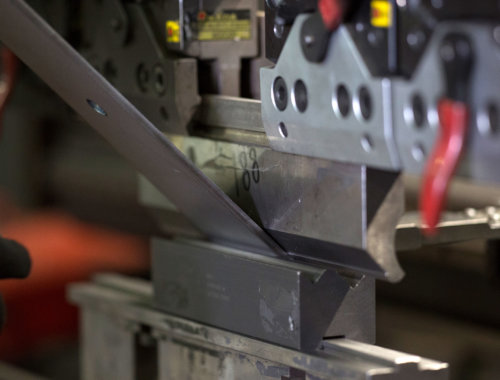
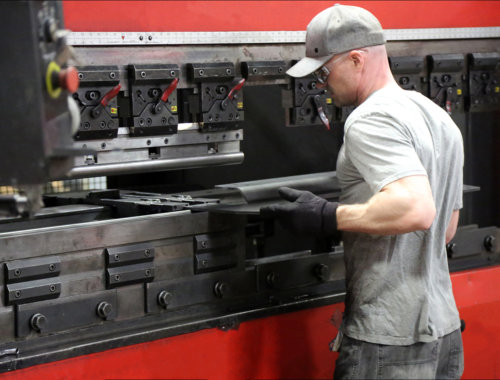
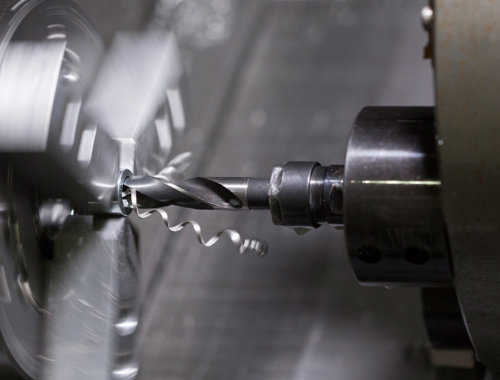
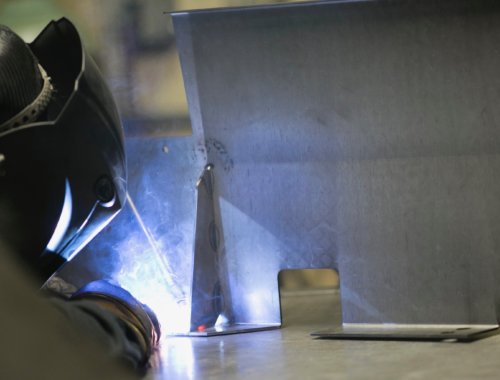
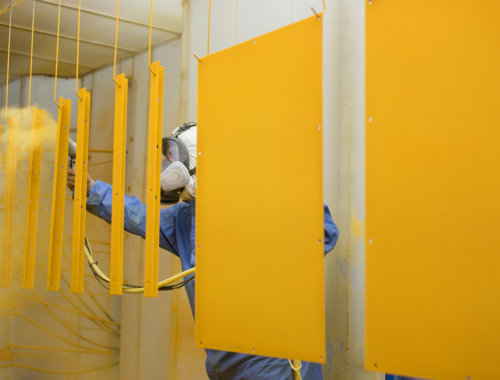
ENGINEERING
First, our Engineering Department determines what the part looks like. Generally, we’re provided with blueprints and 3D models, but sometimes we only get a sample of the piece to be made. In those rare instances, we have to “reverse engineer” the part, determining the processes and materials it will take to make an exact duplicate.
For our example, let’s select a bracket. A drawing is created with Solidworks software and the steps required for our machinery to make the component are programed. An Electronic Demand Profile (EDP), which is essentially a digital version of the part, now exists and can be transmitted out to the machines on the shop floor.
INBOUND LOGistics
Naturally, before any raw materials are delivered to our dock, we have to know what the soon-to-be part will be made of. This is determined by the development of a BOM (Bill of Materials). This is essentially the recipe that includes any and all steps required to fabricate the part. Things that would be included in the BOM are value-added operations and materials consumed in order to successfully manufacture the part.
A preliminary review of the part known as an APQP (Advanced Product Quality Planning) is conducted to ensure any and all quality and engineering requirements for the part can, in fact, be completed by the software, machines and personnel in our plant. It also serves as a double check to make sure we can produce the parts to our customer’s exact requirements.
After these steps are completed, the raw materials can be ordered and delivered to our Inbound Logistics Department where it is inspected for conformance to the customer’s specifications.
laser cutting
Utilizing the EDP, the order for the bracket is first sent to our C02 lasers, where the profile of the piece is cut out of the approved raw material. The bracket is nested with hundreds and thousands of other parts for the optimal yield out of each sheet. For reference, nesting is much like planning how many cookies can be cut out of one piece of dough.
press brake forming
Bends and forms are put into flat pieces sheets of steel using a series of punches and dies. Handling bend lengths up to 9 feet, and with bending forces up to 275 tons, our factory press brakes utilize an electro-hydraulic servo drive system, allowing bends in thicker materials than typically seen. The brakes measure bending angles using specialized sensors, which relay real-time data to machine controls and adjust, if necessary, for enhanced forming accuracy.
The parts are formed virtually in a software program first, so we can see how the raw material interacts with the machine before the part is run. This reduces the likelihood of forming errors and reduces scrap rates.
machining
Precise holes, tapped holes, countersinks, bevels, counterbores and other machined features can be put into parts using our state-of-the-art CNC machining centers. We utilize in-house CNC machining for a variety of reasons, but the main advantages are consistency, reliability and increased throughput. Reduced labor and overhead costs allow us to provide parts with machined features at a more competitive price than if they were outsourced. All of the CNC programming is handled in-house and once the program is downloaded into the machine, the operator downloads a predefined part program, begins the run and then has the ability to run multiple jobs, reducing redundant set up costs.
Our CNC machines allow us to hold extremely tight tolerances up to +/- 0.001”. To make sure the parts meet our customer’s specifications, our standard practice is to check the setup piece, middle piece, and last piece of each run. Tolerances are tested with a variety of measurement devices including micrometers, height gauges, indicators and CMMs (coordinate measuring machines).
welding
Typically, we weld metal components that have been bulk cut on our laser machines and then formed. Welding is used to connect the formed pieces together or add other fabricated parts to complete the basic structure of the object. It can be done on two or more components of steel, stainless, or aluminum.
Our welders are certified for almost any metal-to-metal welding job. Each booth is stocked with both MIG and TIG (tungsten inert gas) units. We also have equipment and certified operators for spot welding and “weld around” work.
For high-volume jobs, we have a Miller PerformArc 350S high output welding system (PA350S), which provides a full spectrum of welding processes and is designed for the rugged demands of robotic industrial welding operations. It provides us the opportunity to utilize automation that benefits both the operator and company by driving maximum throughput.
finishing
The EDP then sends the part to our Finishing Department for oxide removal, deburring, grinding and polishing. We can also arrange for specialized finishing procedures such as Blanchard grinding, zinc plating, black oxide and heat treating.
powder coating
Parts can be coated to any color our customers require on our 7-stage powder coating line. As the name implies, powder coating is applied to the bare metal as a free-flowing dry powder. The spray and metal surface are each given different electrical charges so that the spray is “magnetically” attracted to the metal and adheres to it. The piece is then sent into a cure oven (425 degrees for up to 30 minutes) to form a deep bond or “skin” on the metal. This “electrostatic” application creates a hard finish that is tougher than conventional paint.
assembly
Our fabricated metal part assemblies are custom-built and delivered JIT on a daily basis to assembly lines from our in-house CNC machining, welding, powder coating and finishing operations. The expertise of our assembly managers to customize assembly cells, paired with our investments in superior technology, has allowed us to deliver assembled units to the exact requirements of our customers.
Our assembly capabilities include the insertionof PEM nuts, studs, rubber components and other hardware, riveting, welding, kitting, and custom component assembly.
outbound logistics
Finally, the completed parts are packaged in the most economical fashion to ensure protection during transit. We also conduct freight optimization for our customers as well as book their loads
Components fabricated in the manner described in this article are often part of a bigger mechanism that will take its place on our highways, building and road construction sites, mines and even in the front lines with our military units.
Without the skills and talents of fabrication artists who take raw materials and shape them into their final form, the world would be a much different place.