Laser Precision Receives ISO Recertification Mid-Pandemic
August 30, 2021
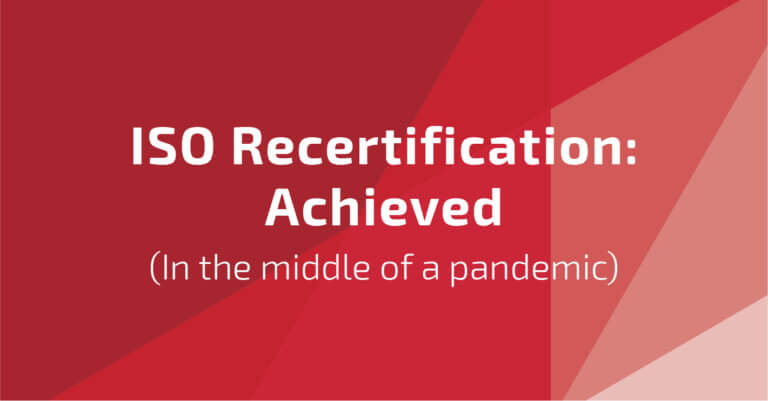
A Quick Recap
In order to achieve certification, an accredited auditing organization (in our case, Perry Johnson Registrars, Inc.) must verify that all of the ISO requirements are being met. The audit checklist consists of seven main categories that are measured to evaluate an organization:
1) Context of the Organization
2) Leadership
3) Planning
4) Support
5) Operations
6) Performance Evaluation
7) Improvement
“One important aspect of ISO 9001 is its process-oriented approach,” said Quality Manager Matthew Keller, who is in charge of the audit. “In addition to looking at a company’s departments and individual processes, ISO 9001 requires that organizations take a ‘big picture’ approach.” In other words, how do processes interact? Can they be integrated with one another? What are the important aspects of products and services? “These are all vital questions that impact our ability to keep our quality and delivery up to par,” Keller said.
An official certificate is issued only after successful completion of the audit and a pledge to maintain the standard’s requirements for continuous improvement. For more background, please read ISO 9001:2015 Certification Confirms Our Commitment to Quality.
A Virtual Audit
The recertification process this year was unusual since it had to be conducted following pandemic safety guidelines. “Under normal circumstances, the audit would be conducted face-to-face on-site over a four-day period,” said Keller. “Because of COVID-19, everything had to be done in a teleconference format.”
Keller says that despite the virtual nature of the audit, it was no less comprehensive than certification in more normal times. “I was able to send our auditor all the documentation required, and we reviewed them just as we would in person,” he said. “We have mini-audits every year, so the process is very familiar to us.”
Thanks to modern technology, even the shop floor audit wasn’t a problem. “I walked around the shop with my phone, showing samples of documentation and conducting interviews with employees,” Keller said. “Even though it was virtual, no aspect of the audit was overlooked. It still took four days and was every bit as stringent as other years.
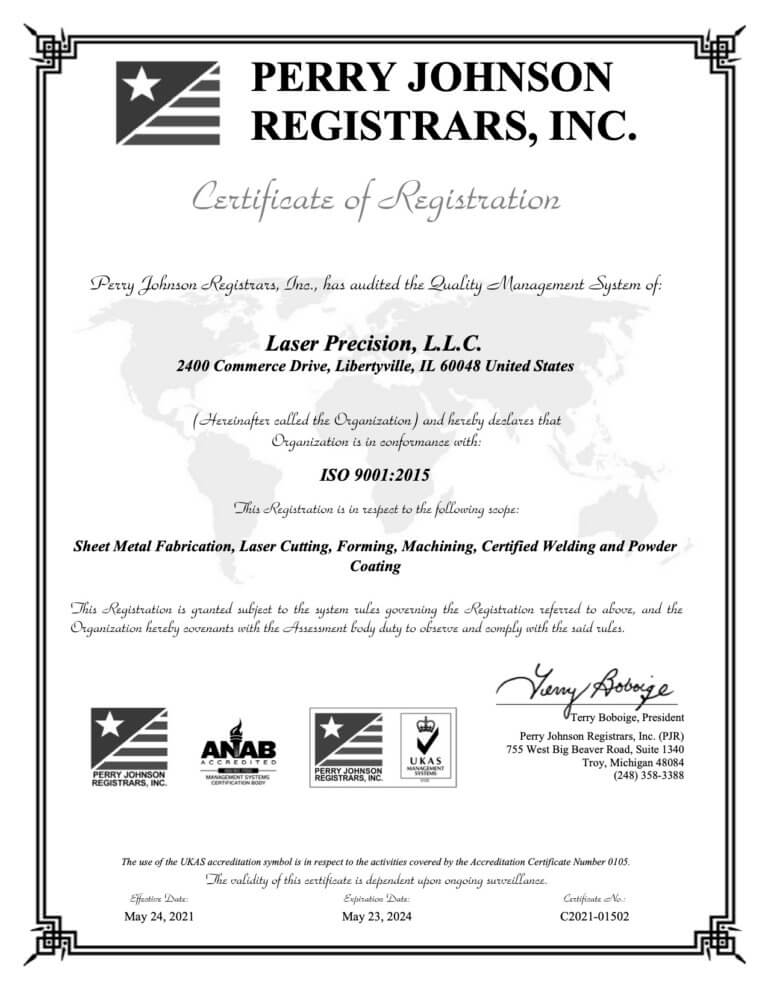
Zero Actionable Issues
Upon completion of the audit, we were notified that we had been recertified with no remedial actions required. In fact, the company hasn’t had an issue that needed to be addressed in over two years. “We follow the ISO guidelines on a daily basis, not just around audit time,” Keller said. “It helps to have an objective third party come in and not only find problems to be fixed, but to confirm that we are doing things right. Companies who don’t go through the audit process may not even be aware of what they’re doing wrong. That’s where ISO certification gives us a competitive advantage.”
If you would like to learn more about how our ISO 9001:2015 certification can add value to your operations, please contact us.