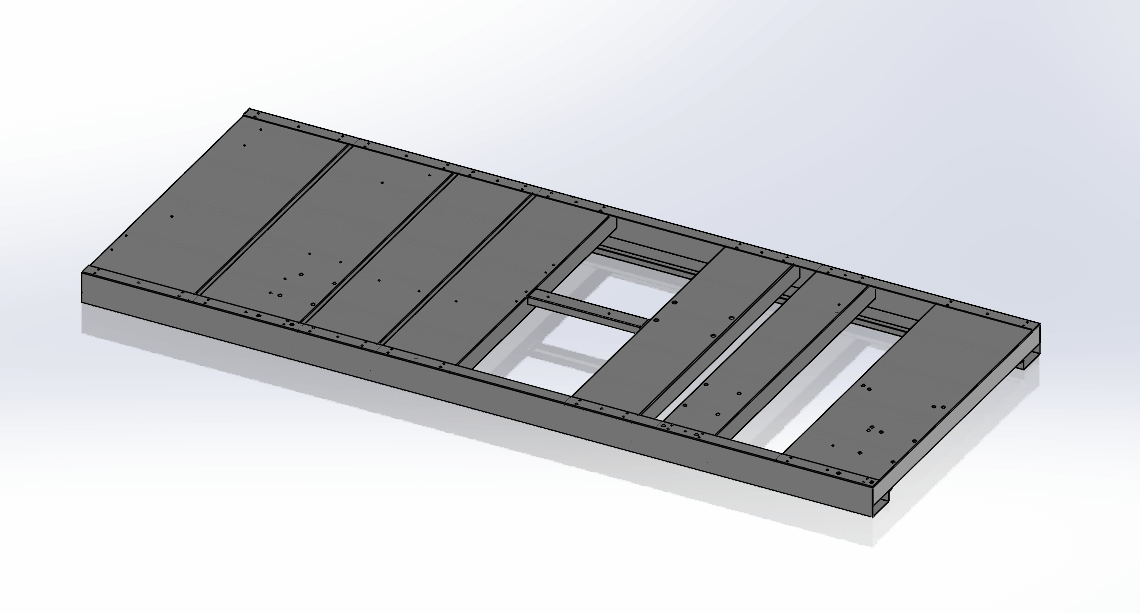
Offline Programming: Another Laser Precision Tool That Ensures On-Time Delivery
June 09, 2021
Once we receive an order, the clock starts ticking. The new job project joins hundreds more that must compete for space on our fabrication equipment. We only have so many machines and operators. How do we maintain an on-time delivery record of 99.92%? In military science, a force multiplier refers to a factor or a combination of factors that gives personnel the ability to accomplish greater feats than without it. Here at Laser Precision, we have our own force multipliers. One of them is offline programming.
Maximum Run Time
Our operators have the ability (and skills) to program jobs on the controller of their machines. But while they are literally programming on the machine (which can be complex and take quite a while), the equipment sits idle. That interval could be spent running another job (or more). To avoid this down time, 100% of our orders are programed offline. We have three engineers who work on this process. The team is responsible for building CAD and SolidWorks models from the customer’s prints. From there, depending on what kind of machine we’re programming for, we’ll use a variety of software that helps us create a CNC program for a mill or turning center, a bending sequence for a press brake, a nesting layout for a laser cutter, a welding sequence for a robotic welder and so on.
All of that software allows us to debug any potential errors and prevent crashes before we manufacture our first part. Not to mention, certain types of software will calculate the best tooling paths to generate a part as efficiency and quickly as possible. Then the offline program goes online by way of servers organized per department where the operators can access and download at the machine level.
A Proven Concept
We have used offline programming for our press brakes, laser cutters and other machine tools for over 15 years. Since we have added automation to our welding department, we are now using it to program welded parts as well. The software keeps track of the robot and the torch, calculates the best path, and even suggests alternate paths as part of its troubleshooting routine.
The Human Element
People are still the most valuable element in our shop. While we work with the latest technology, communication and skill are still vital to our success. The software we use is almost 100% accurate, but on the rare occasion when something is off, our operators are so experienced they can tell immediately. They usually can make a small adjustment on the controller and carry on with the job. Later, they will confer with the engineers to help tweak the program for the next time.
Force Multiplier
To summarize, we use offline programming to expand the amount of work we can deliver with a given number of personnel. Operators can immediately begin to run the next job in the schedule without pausing to program it into the machine. They can also use the software to schedule jobs that require the same tooling sequentially, further reducing setup time required between jobs. The program has been vetted by our engineers before the operators see it, so the job runs smoothly without surprises. This is just another example of how we use technology to better serve our customers and make Laser Precision an exciting place to work for our employees.
If we sound like a place where you might like to work, check out our Careers Page. Manufacturing is a great opportunity if you’re looking for a career change. We’d love to talk to you.